Introduction
As part of exploring options to model jet fans (see our Jet Fan Tutorial), we looked at using a Velocity Patch. The FDS User Guide discusses the concept of a velocity patch in the context of air entrainment by the spray from a sprinkler nozzle. The idea is that the spray droplets accelerate the gas through which they move and a velocity patch gives a way to specify the gas velocity. We sought to apply a velocity patch to a model of a jet fan.
Velocity Patch Background
As described in the FDS User Manual (Section 15.3.3), "The details of the sprinkler head geometry and spray atomization are practically impossible to resolve in a fire calculation. As a result, the local gas phase entrainment by the sprinkler is difficult to predict. As an alternative, it is possible to specify the local gas velocity in the vicinity of the sprinkler nozzle."
A velocity patch consists of:
- A bounding volume
- A cartesian point (XYZ)
- Polynomial coefficients that define the velocity using a second order Taylor expansion about the cartesian point XYZ.
The polynomial is specified by the coefficients:
- P0 - the value of the velocity component (k)
- PX(1:3) - the first derivatives at cartesian point XYZ
- PXX(1:3,1:3) - the second derivatives at cartesian point XYZ
If we want a constant velocity, we only specify P0. The first line of the FDS input in Figure 1 defines the velocity component (in this case the X direction) and the constant value, P0. The second line defines a timer that activates the patch. The third line defines the geometry of the patch and links the patch to the previous data. By default the point XYZ is the center of XB, but as will be shown below, you can add a point definition to this line to shift the center of the expansion.

For a parabolic velocity in the X direction that varies in the Y-Z plane, the Taylor expansion simplifies to:
The plot shows the velocity for a patch that extends from Y=-1
to Y=1
and Z=-1
to Z=1
, with latex:[TCP_{mpp}] and \(P_{22}=P_{33}=-10\).
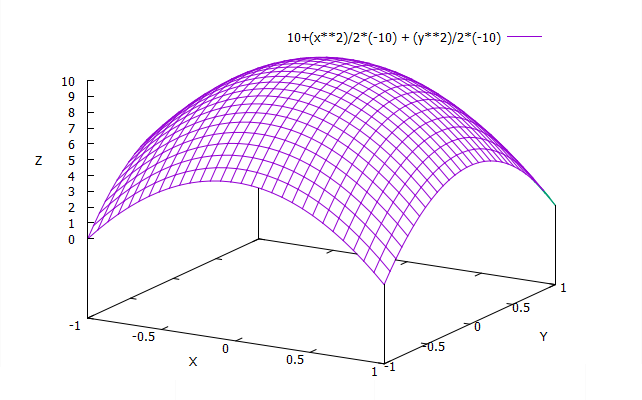
This was tested in PyroSim using the following FDS input data:

which resulted in the contours shown in Figure 4 that match the expected results.
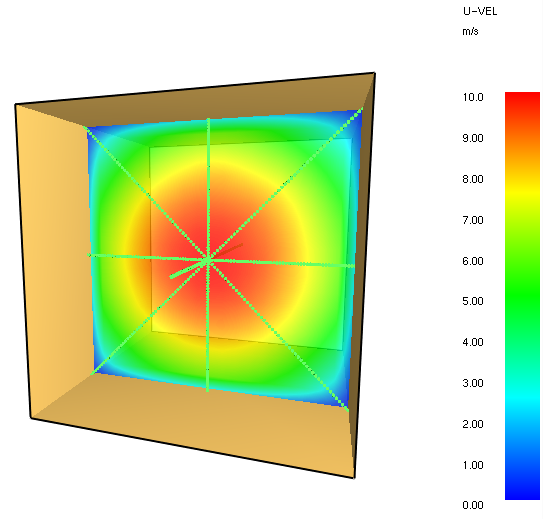
To demonstrate shifting the XYZ point for the Taylor expansion from the center to the edge at Y=1
, we add XYZ data to the velocity patch device:

This results in the countours shown in Figure 6:
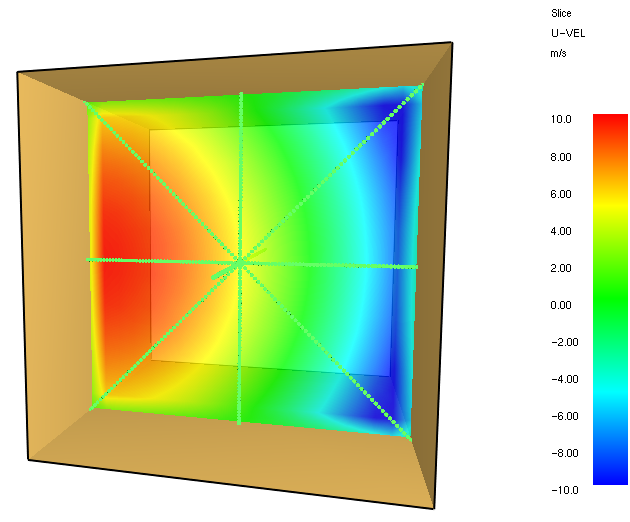
Applications
The velocity patch makes it possible to define the gas velocity components within a given volume. For a sprinkler, this allows the user to specify the gas velocity caused by the spray droplets. We tested a model of a jet fan, shown in Figure 7 by making a shroud of thin obstructions and specifying the velocity of the gas along the axis of the fan using a velocity patch.
In the end, using a velocity patch to model a jet fan is probably not the best approach, but it does demonstrate one uncommon feature of FDS.
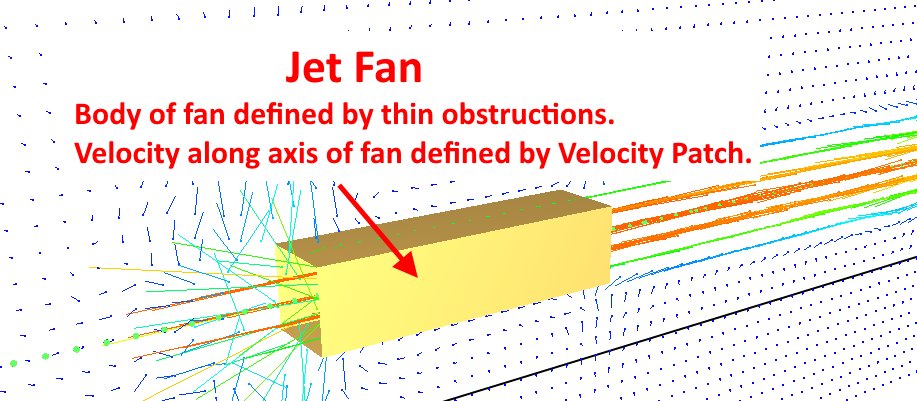
To download the most recent version of PyroSim, please visit the the PyroSim Support page and click the link for the current release. If you have any questions, please contact support@thunderheadeng.com.
Related Tutorials
Tutorial demonstrating how to model jet fans in Pyrosim.
(Legacy) Tutorial to experience the fundamental features of PyroSim
Tutorial demonstrating how to verify HVAC Pressure Drop in Pyrosim.
Tutorial demonstrating how to model critical velocity in Pyrosim using the example of a tunnel fire.
Tutorial demonstrating how to model Radiation and Convection on Surfaces in Pyrosim.
Tutorial demonstrating how to use PyroSim/FDS to Maximize Solar Panel Convective Cooling.
Tutorial demonstrating how to model Smoke Visibility and Obscuration in Pyrosim.
Tutorial demonstrating how to model a pressure relief vent in Pyrosim.